Sustainability / Social Report / Creating Attractive WorkplacesOccupational Health and Safety
Basic Approach
To ensure the safety of its workplaces, the Daicel Group promotes various measures such as conducting risk assessments of all its activities, including R&D, manufacturing, and logistics, in accordance with the Daicel Group Basic Policies for Responsible Care. We have also established medium and long-term goals and carry out the CAPD*1 cycle as part of a continual effort to improve the occupational health and safety of our employees.
Placing the highest priority on safety in manufacturing, all workers and management at our business sites and partner companies (contractors)*2 work to improve the foundation of our production sites.
- *1Instead of a Plan, Do, Check, and Act (PDCA) cycle, the most widely known approach to continuous improvement, Daicel has adopted a CAPD improvement cycle to avoid the risk of overlooking crucial facts and realities that often lie hidden in the initial planning stage.
- *2Partner companies (contractors) are companies outside the Daicel Group that engage in various operations primarily at our business sites.
Promotion System
Through our responsible care system, which is supervised mainly by the Responsible Care (“RC”) Committee, health and safety management supervisors from each business site leads our efforts to improve the quality of health and safety management at our business sites. We implement DAICEL Production Innovation for process-based production at our domestic business sites. For assembly-based manufacturing done at Group companies in Japan and overseas, we utilize the approach of the Toyota Production System based on DAICEL Production Innovation, and operate a labor health and safety management system tailored to each business site. Furthermore, some of our domestic and overseas Group companies are ISO45001 certified.
DAICEL Production Innovation
This production system goes back to the basics and focuses on human-oriented manufacturing. By systemizing the skills and know-how of experienced staff and enabling everyone to put them to practical use, it endeavors to achieve a broad range of results that include:
(1) Occupational health and safety/process safety and disaster prevention, and stable operations
(2) Dramatically higher productivity
(3) Substantially lower manufacturing costs
(4) Smoother, more finely-tuned operations and quality stabilization
(5) The passing on of skills and techniques and human resource development
(6) Energy conservation
Also, we regularly conduct meetings of environmental and safety division supervisors, which are attended by safety management supervisors from each business site and members of the Responsible Care Center (“RC Center”) of the Safety and Quality Assurance Headquarters. In these meetings, members share information and discuss RC-related problems such as occupational health and safety, process safety and disaster prevention, and environmental conservation, as well as the content of revisions to laws and regulations such as the Industrial Safety and Health Act. In addition, during considerations of major issues, members confirm and discuss progress and issues concerning the RC Yearly Activity Plan, including occupational health and safety, which each business site formulates.
Various councils led by partner companies (contractors) and the Environment and Safety Division have also been established at each business site to confirm and discuss all manner of policies to ensure safety.
Initiatives toward Zero Occupational Accidents
The Daicel Group has set zero major occupational accidents as a KPI in its materiality, and carries out the CAPD cycle and takes a variety of measures, including those below, to eliminate all serious workplace accidents.
■Practicing 3S, HH, and KY
In Japan, all business sites, including those of our partner companies (contractors), practice the 3S methodology of —Seiri (Sorting), Seiton (Setting-in-Order), and Seisou (Shining)—as well as HH (near-miss reporting)*1 and KY (work injury prediction) as basic practices in order to improve the foundation of our business sites and prevent the occurrence of problems.
■Before/After (BA) approach
We use a BA (Before/After) approach: Cases identified through this process as needing improvement are noted as “before” situations, and “after” situations are after improvements have been made. These workplace improvement initiatives involve employees consulting with their supervisors using BA sheets and then carrying out human and physical countermeasures. Progress with improvements is visualized as an after-improvement rate, and details are shared at health and safety meetings attended by employees and management at each business site. Workplace improvements help prevent problems, prevent quality defects, and improve productivity.
■Looking to the future while respecting the past
We believe in “looking to the future while respecting the past,” aiming to foster a safety culture while preventing the recurrence of workplace accidents. We look back on workplace accidents and process-related accidents arising from unsafe behavior and the neglect of the basics, work to prevent recurrence, and raise employees' safety awareness.
Every month, the RC Center shares information about workplace accidents and process safety incidents that occurred the previous fiscal year with the workplace where those incidents occurred. This information helps employees at these workplaces review and make themselves aware of the incidents to avoid complacency in preventing their recurrence. In this way, both employees and managers work to prevent similar accidents from happening.
In FY2024/3, we and our partner companies (contractors) continued our efforts of FY2023/3 and worked toward our goal of eliminating serious workplace accidents, including chemical injuries, caught in, on or between, falls, and heat stroke. As a measure to eliminate chemical injuries, caught in, on or between accidents, and falls, we have continued promoting initiatives for pre-work safety assessments through the Whiteboard KY Sessions*2, a system shared by all business sites. For heat stroke, we have made sure employees can readily replenish drinking water and mineral supplies, set up rest areas, enforced mask usage rules, and encouraged the use of equipment to prevent and treat heat stroke. In order to prevent health problems and chemical injuries caused by chemical substances, we are working to reduce the risk of hazards and dangers in work by conducting chemical substance risk assessments and complying with the revised Industrial Safety and Health Act (new chemical substance regulations).
In FY2024/3, there were 44 occupational accidents for the entire Group, consisting of 26 resulting in lost workdays and 18 that did not. There were no fatal accidents, and 1 serious accident resulting in permanent disability. In the event of an occupational accident, an overview of the accident is shared with the RC Center through the "Incidents Database" promptly after they occur in accordance with internal rules. When investigating the cause and examining temporary and permanent recurrence prevention measures, a problem review sheet*3 is used, and the relevant parties proceed with the examination, and recurrence prevention measures are determined. This information is also shared horizontally with other business sites through the database and used to prevent similar accidents.
- *1Near misses: Activities that are recorded as events that nearly became accidents or incidents, and whose causes are investigated by all involved. Eliminating the causes of near misses makes for safer workplace environments.
- *2Aiming to ensure that work risks have been exhaustively identified, these sessions involve workers, supervisors, and experts using a shared format board to discuss and predict work-associated risks in advance, and confirm measures to mitigate them.
- *3This is a proprietary tool where technical experts from the relevant department as well as other departments jointly investigate and confirm the objective and detailed facts of the problem events that occurred on-site, such as malfunctions and problems, repeatedly verify the hypotheses with technical evidence and facts, identify the root cause, and determine countermeasures to prevent recurrence.
Number of Occupational Accidents (Daicel Group)
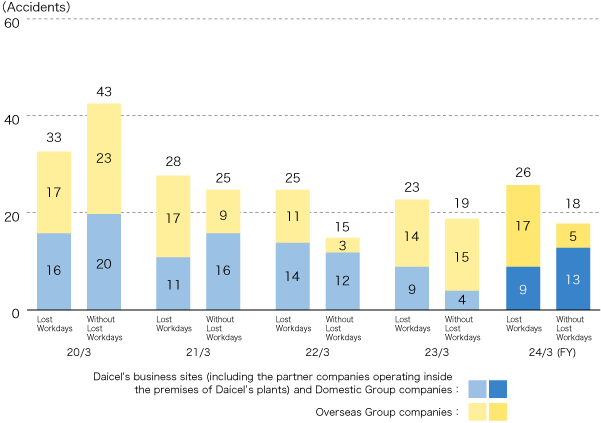
Lost Workday Accident Frequency Rate* (Daicel Group)
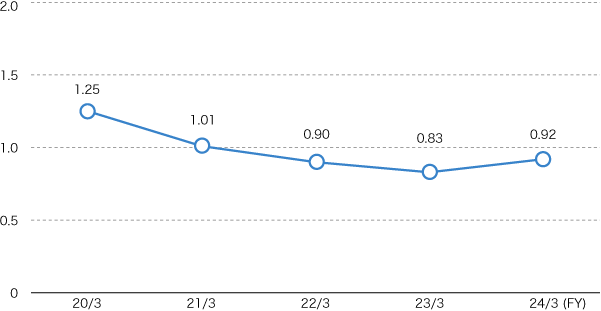
*Lost Workday Accident Frequency Rate = number of people involved in an accident resulting in lost workdays / total actual working hours × 1 million hours
ESG DataRefer to page 3 "Occupational Health and Safety."
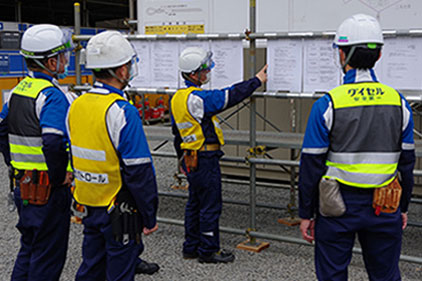
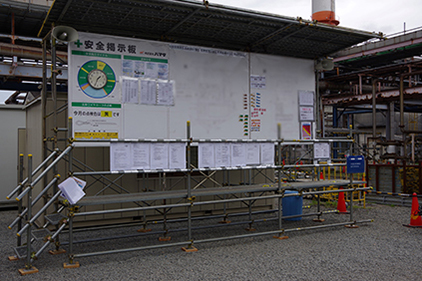
Patrols to ensure against heatstroke and injuries from hazardous substances
Initiatives to Improve Occupational Health and Safety
Safety Education for Employees and Partner Companies (contractors)
The Daicel Group formulates its own training programs and provides necessary technologies and skills for employees, as well as regular safety education.
■Initiatives at the Operation Training Center (TRC)
In order to provide training on technology and knowledge related to chemical plants, the Group set up the Operation Training Center (TRC) where all staff learn about the background and goals of the mechanisms and rules created in light of past incidents. Employees also use special equipment to engage in hands-on risk training that includes experiencing crush accidents, static electricity, solvent and dust explosions, pressure, and exposure to caustic liquids. In FY2024/3, 495 people took training at the TRC, and a total of 9,090 people have taken training since the Center was founded in 2002.
■Initiatives at each business site
Each business site receives training in using manufacturing technologies particular to their work processes, as well as training in occupational health and safety, environmental conservation, and chemicals management. Through TRC branch offices at each site, employees also take part in information sharing and simulation training for incidents that happened at business sites in the past. We review the curriculum for education and training every year, taking into account education using VR and newly arising issues, and continuously implement education and training in accordance with the annual plan. More than 21,000 people in total took training through TRC branch offices at each business site in FY2024/3.
Furthermore, for all cooperating companies and construction-related personnel who enter business sites, we provide education on the safety policy, safety measures, and other relevant information, and we also conduct site-specific safety training along with confirming business site safety rules and their level of understanding.
Furthermore, business partners and construction workers receive safety training specific to that site to confirm that they understand all safety rules. In addition, at workplaces where incidents occurred in the past, notices containing information about the events are posted to prevent complacency and raise awareness. Also, through the Occupational Accidents and Process Safety Incidents Database, TRC branch offices share information about incidents, as well as their causes and prevention measures, with top management and business sites where those types of incidents have not occurred.
Furthermore, in career development training for newly promoted employees, conducted as part of our human resource development program, we educate employees on our approach to disaster and risk management by citing the history of the explosion and fire that occurred at the Sakai Plant in 1982, using newspaper articles from that time and video footage to reinforce the importance of placing safety first in manufacturing. In the human resource development program for engineers to exercise their specialized skills, we organize seminars on assessment methods, including HAZOP,* and total and technical assessments, as well as the environmental management system.
*Hazard and operability (HAZOP) is a qualitative analysis method for providing feedback on potential hazards and operability issues in the design process.
Creation and Distribution of “The Essence of Safe Operations” and the “Basic Internal Rulebook on Construction Work”
The Daicel Group has numerous in-house rules on manufacturing safety, including the "Essence of Safe Operations" and "Basic Internal Rulebook on Construction Work," established in FY2014/3 to enable all front-line operators of the Group involved in manufacturing to be aware of, think about, and act to ensure safety on the same basis.
■Essence of Safe Operations
We created pocket-sized versions of these documents to allow workers to check, anywhere and at any time, the key points of safety rules that apply in the field, including information about the types of protective gear, how to use it, and how to use tools. In 2018, we issued the third edition, which includes more diagrams and photos so as to facilitate reading and understanding, and in 2020, the fourth edition which includes rules for preventing electrostatic accidents and the appropriate wearing of new uniforms was issued. In April 2022, we published the fifth edition of the leaflet, making changes necessitated by revisions to the Static Electricity Accident Prevention Rules (Powders and Liquids) and adding in content about safety when working at heights and other matters.
In April 2024, in accordance with the revision of the Industrial Safety and Health Act, we reviewed and added items related to the strengthening of voluntary management of chemical safety and published the sixth edition.
■Basic Internal Rulebook on Construction Work
There are two versions of the Basic Internal Rulebook on Construction Work, the Safety Version and the Quality Version. The Safety Version is a compilation of Daicel’s unified basic rules related to construction work, formulated based on feedback from field personnel. We created the rulebook based on our belief that complying with these rules is essential, not only to ensure one’s own safety but also to ensure the safety of colleagues working at the same site. The Quality Version focuses exclusively on rules aimed at preventing a recurrence of serious incidents resulting from defects in construction quality. It was created with the intention of encouraging employees to gain a deep understanding of the key points for ensuring construction quality and to comply with the rules. In April 2024, we issued a revised edition of the leaflet containing updated information.
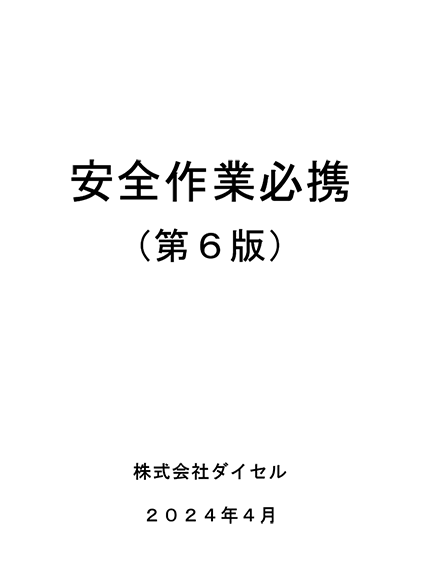
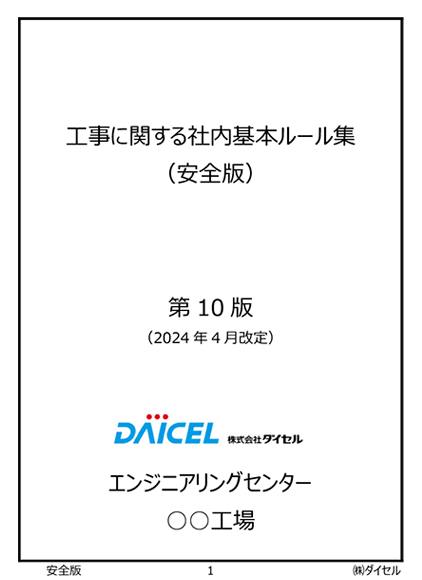
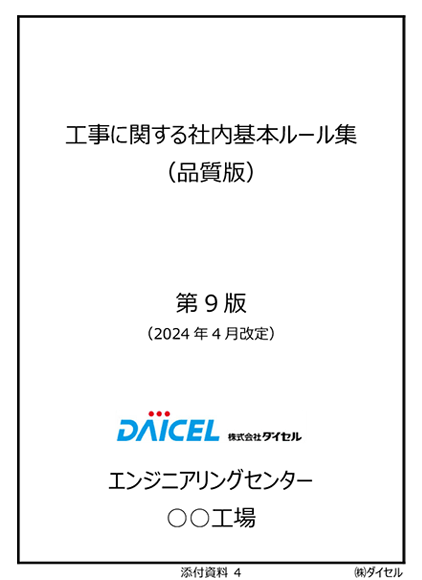
Safety Programs for Partner Companies (contractors) and Business Partners
We strive to ensure the safety of each business site by educating not only Daicel Group employees but all workers of partner companies (contractors) who are involved in manufacturing and construction work. To raise safety awareness, we continuously provide education on safety rules related to occupational health and safety process safety, and disaster prevention on a regular basis, such as when workers enter the worksite for the first time or before undertaking periodic repair work.