Sustainability / Social Report / Customer Satisfaction and Safety AssuranceEnhancing Product Quality
The Daicel Group, adhering to its Quality Policy, strives to deliver customer satisfaction and safety assurance through reliable manufacturing and active information disclosure.
Quality Policy for Daicel Group
Each member of the Daicel Group promises to deliver safe and quality products and services that can be used with confidence by customers. In order to realize this policy, we undertake the following actions.
- We listen to customer requirements and deliver trust and satisfaction.
- We clarify and seek to achieve the required quality.
- We obey laws and regulations.
- Each member looks at matters from the customer’s perspective and undertakes actions on their own initiative.
Established April 6, 2016
Quality Management System
Sales, marketing, and development are handled by SBUs in our company, while SCM Headquarters oversee raw material procurement, production planning, as well as shipping and distribution. Manufacturing is the responsibility of the six key factories and production subsidiaries. Together, they form our quality management system, which is followed by all group companies.
Apart from our annual management reviews, we also have monthly or bi-monthly review meetings (such as Quality Assurance Committees, etc.) to measure the progress made towards quality objectives and effectiveness of activities, with a view to achieving continuous improvement. Also, the corporate departments provide audit reports and quality white papers for decision making purposes by top management, in addition to the monthly reports.
Where necessary, we obtain certifications for quality management systems (QMS) standards such as ISO9001, notably in our manufacturing sites.
Our Structure for Quality Management
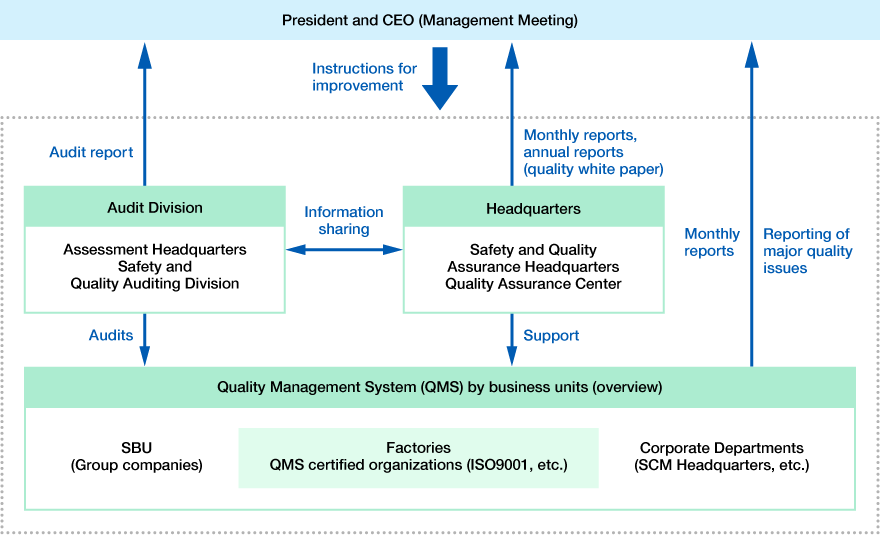
Certification Status
The Daicel Group has obtained Quality Management System (QMS) standards starting from the ISO9001 to meet the demands and expectations of our customers. Some of our notable QMS standards besides the ISO9001 include the following.
[Examples of certifications]
- IATF 16949 for the automotive sector
- ISO 13485 for the medical equipment sector
- ISO 22000 and FSSC 22000 for food safety management
Initiatives for Improving Customer Satisfaction
The Daicel Group investigates the needs and expectations of our customers, as well as the market trends and other factors. We then work towards planning and delivering new products.
For design and development, we translate the functionality required by our customers into performance and work to bring it to market. We also undergo third-party certifications if required, such as DOT certification to evaluate the safety of hazardous material transportation, UL certification to evaluate flame retardancy of plastic materials, and CoC certification for proof of a sustainable use of forest resources.
In our production process, we follow a pre-determined procedures to keep the stability of our production and maintain traceability from raw material to finished products.
We diligently inspect our products and only ship those that meet our high standards, in order to prevent the release of defective items to the market. Should any defective products be discovered, we will take appropriate corrective measures to prevent a recurrence.
In product sales, we disclose data of the safety of our products and precautions required for their safe handling. For chemical products, we provide an SDS.* When there is a change in equipment, material, method, or specification that involves products on the market, we look for the impact of the change upon quality. Besides, depending on the details of the contract, we will contact our customers in advance to explain changes and offer an initial production sample for evaluation at their request.
In July 2022, we discovered inappropriate behaviors concerning UL certification for some resin products sold by Daicel Miraizu Ltd., one of our group companies. The certification was revoked, and we notified the public about the incident. We established an investigation commission with our independent Outside Audit & Supervisory Board Member as the chair. The committee is made up of outside experts with no stake in our company. In December of the same year, we received a report with recommendations of measures for recurrence prevention. We published the report in January of the following year. We take this incident sincerely and solemnly, and we take all measures to prevent its recurrence.
Also, there was no case of UL certification revocation in FY2024/3.
*SDS: Short for Safety Data Sheet, this document provides information on the properties, safety, and handling of chemical substances.
Responding to Customer Feedback
We run a company-wide database of customer complaints and inquiries within our group. We share their details with relevant parties in the company in real time. Along with information collection, this helps us to prevent any recurrence.
We take care to provide rapid feedback in response to complaints and inquiries. We look immediately for possibility of defective products being released. Once this is done, we will report and explain our findings to customers.
We identify the root causes of the complaints, make sure to take corrective actions to prevent recurrence. When necessary, we roll out the information across the organization to prevent similar case from occurring again.
Discrepancies and corrective actions, including customer complaints, are subject to the management reviews of each organization for effective decision-making.
Customer Complaints about the Daicel Group*
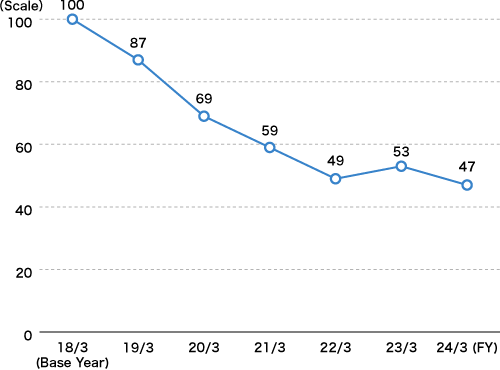
- *Shows the change in the number of customer complaints on a scale where data for FY2018/3 is 100.
- *Scope: Daicel Corporation, Dainichi Chemical Co., Ltd., Daicel Pyrotechnics Ltd., Daicen Membrane-Systems Ltd., Daicel Miraizu Ltd., Daicel Pack Systems Ltd., Daicel-Allnex Ltd., Daicel Aboshi Sangyo Co., Ltd., DM Novafoam Ltd., and Polyplastics Co., Ltd. (includes overseas companies), Polyplastics-Evonik Corporation, Daicel Nanning Food Ingredients Co., Ltd., Shanghai Daicel Polymers, Ltd., Daicel Safety Systems Europe Sp.z o.o., Daicel Safety Systems Americas, Inc.、Daicel Safety Systems (Jiangsu) Co., Ltd., Daicel Safety Technologies (Jiangsu) Co., Ltd., Daicel Safety Systems Korea, Inc., Daicel Safety Systems (Thailand) Co., Ltd., Daicel Safety Technologies (Thailand) Co., Ltd.
- *Applicable companies added in September 2021: Chiral Technologies Europe S.A.S., Chiral Technologies, Inc., Daicel Chiral Technologies (China) Co., Ltd., Daicel Chiral Technologies (India) Pvt. Ltd., Daicel Arbor Biosciences
- *Applicable companies added in April 2022: Xi’an Huida Chemical Industries Co., Ltd., Xi’an Da-an Chemical Industries Co., Ltd., and Ningbo Da-an Chemical Industries Co., Ltd.
- *Applicable companies added in or after October 2022: Daicel Beyond Ltd.
- *Applicable companies added in April 2023: Daicel Safety Systems India Pvt Ltd, Polyplastics (Nantong) Ltd.
- *Daicel Pyrotechnics Ltd. data is included up to the end of February 2024.
Rate of Initial Response to Customer Complaints within 24 Hours
FY | 2022/3 | 2023/3 | 2024/3 |
---|---|---|---|
Rate of initial response within 24 hours (%) | 63 | 88 | 89 |
Average number of days to initial response at production sites | 2.2 | 0.7 | 0.7 |
- *Applicable sites: Daicel production sites in Japan
- *The target rate of initial response within 24 hours is 100% by FY2026/3
Internal Education and Training
In our common quality education, we provide grade-level training on quality control and quality management according to position, role, and title to new employees and promoted employees. Moreover, to improve the quality literacy level of our group, we also organize open-call training on quality control targeting various types of jobs, and cultivation of internal auditor.
The graph below shows training sessions held in FY2024/3.
Common Training Sessions Conducted in FY2024/3
Scroll left or right
Names | Target audience (including our group companies) |
Contents | Number of Participants (persons) |
---|---|---|---|
Grade-level training | New employees | Quality control, quality management, etc. | 590 |
Union members in technical and administrative fields | |||
Promoted personnel (union members) | |||
Newly appointed leaders (managers) | |||
Open-call training | All employees | Quality control (by job function, including research and development, sales, procurement, and inspection; includes corrective actions) internal auditor cultivation, etc. | 242 |
Moreover, we conduct required trainings at each business site with quality management systems in place, such as the Quality Dojo of the Harima Plant.
Risk Management for Product Safety
The Daicel Group, operating in sectors like pharmaceuticals, cosmetics, food, and automobile safety equipment, carries out risk assessments to deliver customer satisfaction and safety assurance.
From the planning stage through to mass production, we hold Product Safety Advisory Committee as necessary, while also incorporating the opinions of external experts, to extract the problems by identifying and evaluating the risks. Furthermore, on all the above products, we conduct a Product Crisis Assessment before their launch on the market to identify and assess the product safety risks by presetting and deciding responses (crisis response measures) in preparation for when an incident happens.
If we suspect a huge quality problem (improper quality practices, product liability incident or product accidents, customer product recalls, etc.) after starting the manufacturing or selling, we make an immediate report to the management. If company-wide support is required, we will set up the s Emergency Response Team for Major Quality Issues and prioritize victim relief.
In FY2024/3, there were no product safety accidents that negatively affected customers’ physical wellbeing, life, or property.
Process Flowchart for Responding to Serious Product Deficiencies
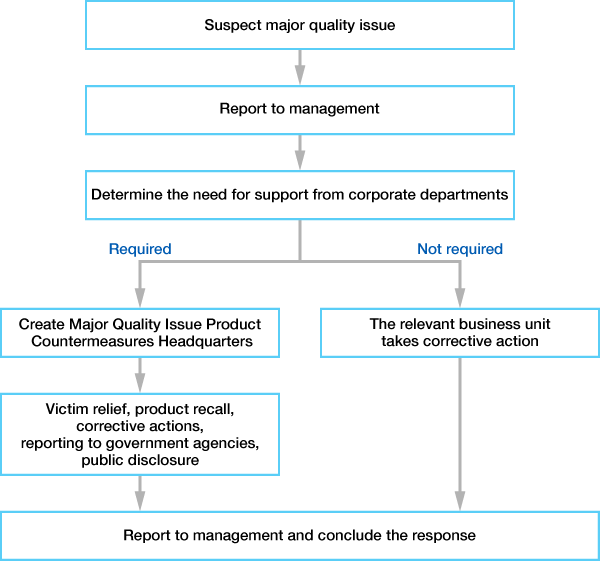