Sustainability / Social Report / Customer Satisfaction and Safety Assurance Distribution Safety
Basic Approach
Daicel Group works with one of its Group companies, Daicel Logistics Service Co., Ltd., to ensure safe distribution and quality management.
As for distribution safety, we aim to achieve zero logistics accidents, occupational accidents and at-fault traffic accidents by adhering to the Daicel Group Basic Policies for Responsible Care. In assuring quality, we are guided by the Quality Policy for the Daicel Group and strive to achieve our target of “taking responsibility as a logistics contracting company by quickly and sincerely responding to complaints and accidents related to logistics to earn the customer satisfaction (CS) of distributors.”
Promotion System
We promote initiatives for ensuring distribution safety and quality with a focus on Daicel Logistics Service, given that the company handles most of the distribution operations of the Daicel Group.
Daicel Logistics Service implements and operates its quality management system in accordance with ISO 9001 using a CAPD*1 cycle. As a distributor, Daicel Group checks on the status of the initiatives of Daicel Logistics Service and engages in resolving any issues as part of its responsible care activities together with Daicel Logistics Service.
In addition, we are working to improve logistics efficiency and energy conservation to address logistics problems in 2024*2 and achieve carbon neutrality by 2050.
- *1Instead of a Plan, Do, Check, and Act (PDCA) cycle, the most widely known approach to continuous improvement, Daicel has adopted a CAPD improvement cycle to avoid the risk of overlooking crucial facts and realities that often lie hidden in the initial planning stage
- *2Starting from April 1, 2024, the overtime exemption regulations for automobile driving operations have been abolished, and with the application of the annual limit of 960 hours, further concerns about a shortage of drivers in the transportation industry are arising
Daicel Logistics Service Co., Ltd. Quality Policy (Japanese text only)
Safe Product Transport and Logistics Quality Management
Ensuring Safe Product Transport
Daicel Logistics Service promotes safe transport by upholding the targets of zero logistics accidents,*1 zero occupational accidents and zero at-fault traffic accidents. Annual distribution safety targets are set by each distribution center, which serve as logistic hubs. Progress on achieving the targets is reviewed each month by the Safety and Quality Committee, which comprises the heads of each center and department, and improvements are made, including revising the targets according to the circumstances.
In FY2024/3, while there were zero logistics accidents, there was one occupational accident. We investigated the causes of the accident and took preventive measures to address both physical and human errors.
Basic Initiatives
- 1Corrective measures for work system and work procedure flaws
- 2Sharing case studies and countermeasures at Safety and Quality Committee meetings
- 3Expand the educational curriculum taught by experienced staff (at the Safety and Quality Training Center)
- Training to prevent workplace accident recurrence based on past incidents, and loading and unloading training
- Drills simulating leakages
- Education on the causes of at fault traffic accidents and on dangers when driving based on past incidents
- 4Installation of drive recorders to analyze accidents, and use of video footage to pass on skills of veteran workers for training
- 5Education on the hazards of chemical substances noted on SDS*2 and GHS*3 labels
- *1Accidents such as fires, explosions, leakages, discharges and losses associated with hazardous products (hazardous materials, poisonous and deleterious substances, high-pressure gas, environmental pollutants, and combustibles)
- *2Safety Data Sheet, a document that provides information about the characteristics, safety, and handling of chemical substances
- *3Globally Harmonized System of Classification and Labelling of Chemicals, an internationally standardized set of rules that provides standards for classifying chemicals based on hazards and content to note on labels and safety data sheets
Daicel Logistics Service Safety Targets:
Zero logistics accidents, zero occupational accidents, and zero at-fault traffic accidents
FY2024/3 Results:
- Achieved zero logistics accident (no change from FY2023/3)
- One occupational accident (down two from FY2023/3)
- Zero at-fault traffic accidents (down three from FY2023/3)
For Achieving a Mindset and Behavior Focused on Safety
We seek to prevent logistics accidents, occupational accidents and at-fault traffic accidents by consistently implementing initiatives designed to firmly establish safety awareness and behavior among workers.
Major Initiatives
Prevention of logistics accidents |
Safety education based on Transport Safety Management conducted at each distribution center (once a month)
|
---|---|
Prevention of occupational accidents |
Health management for safe transport (daily)
|
Prevention of at-fault traffic accidents | Operation managers at each distribution center provide education on safe driving to drivers using dashcam video of their actual transport operations (as needed) |
Initiatives for Ensuring Safety during Transport and Storage of Hazardous Materials
In addition to transporting hazardous materials, Daicel Logistics Service handles storage of ordinary goods (designated combustibles and poisonous substances), ambient temperature hazardous material storage (Type 4 hazardous substances, Type 5 hazardous substances, and poisonous substances), and fixed temperature storage (cold) storage (Type 4 hazardous materials and poisonous substances). Hazardous materials are transported and stored in accordance with Japan’s Fire Service Act and the United Nations Recommendations on the Transport of Dangerous Goods (Orange Book)*1. Daicel Logistics Service also implements its own safety measures in an effort to prevent accidents.
Major Initiatives
- Formulate and make effective use of operation manuals and check lists on the transport, loading and unloading of dangerous goods.
- When filling dangerous materials, comply with instructions on labels (displayed on the product and at the storage location) and standard operating procedures for storage and handling.
- When transporting dangerous materials, carry Yellow Cards*2 as an obligation.
- Provide education on the physical properties of dangerous materials during safety meetings (around once a month).
- Provide training for skilled experts and drivers at the Safety and Quality Training Center (around 15 times a year).
- Provide logistics safety training for the transport, loading, and unloading of hazardous materials for 20 business partners*3 (once a year for each company)
- Logistics safety audits for business partners
- In addition to legally-mandated inspections for transport equipment, create a planned upkeep program for Daicel Logistics' own inspections and maintenance
- *1Recommendations compiled by the United Nations and revised every two years with the aim of harmonizing national regulations and international rules on the transport of dangerous materials such as gunpowder, gases, liquids and solids.
- *2Listing emergency responses to be taken by drivers, firefighters and police officers in the event of an accident.
- *3Companies outside the Daicel Group to which Daicel Logistics outsources various logistics-related operations
Response to Distribution Accidents
Daicel Logistics Service has established its emergency response and contact lists based on its Emergency Response Regulations. The company also conducts internal emergency reporting drills at least three times a year to remain prepared for emergencies.
Managing Logistics Quality
Daicel Logistics Service promotes stringent management of logistics quality by following its policy of “taking responsibility as a logistics contracting company by quickly and sincerely responding to complaints and accidents relating to logistics to earn the customer satisfaction of the distributors.” At its monthly meetings, the Safety and Quality Committee reviews incidents involving logistics*, analyzes causes, and examines the effectiveness of response measures as a means to eliminate logistics issues.
The number of incidents related to logistics in FY2024/3 dropped by around 20% compared to the reference year of FY2017/3, increasing approximately 6% from FY2023/3.
As almost all incidents had a precedent, recurrence prevention measures were reviewed, and personnel were trained and made aware of the measures.
Number of Logistics Issues
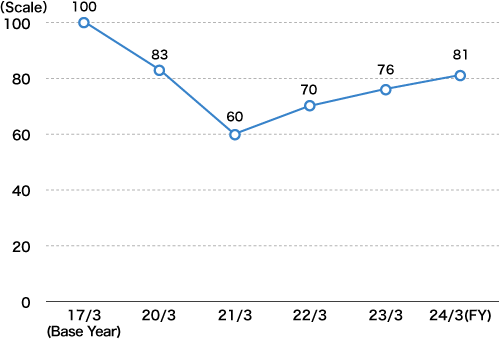
*Overall term for logistics accidents, complaints, shipping and delivery errors, contamination, occupational accidents, traffic accidents and on-site accidents.
Promotion of the White Logistics Movement
Agreeing to the White Logistics Movement, launched by the Ministry of Land, Infrastructure, Transport and Tourism (MLIT), Ministry of Economy, Trade and Industry (METI) and Ministry of Agriculture, Forestry and Fisheries (MAFF), Daicel submitted a declaration of its voluntary activities to the secretariat of the movement together with Daicel Logistics Service.
Daicel's Code of Conduct
- 1Suggestions for and efforts to make logistics improvements: We will faithfully discuss and respond to requests for proposals and cooperation concerning improvements from suppliers and distributors.
- 2Usage of pallets, etc.: We will work to reduce loading and unloading time by using pallets, cage carts, reusable shipping cartons, etc.
- 3Separation of highway transport operations and cargo collection and shipping operations: We will faithfully discuss and respond to requests for advice from distributors concerning the separation of highway transport operations and cargo collection and shipping operations.
- 4Making improvements to shippers' facilities: We will shorten cargo wait time and loading and unloading time by making improvements to distribution facilities that include consolidating warehouses.
- 5Usage of expressways: We will faithfully discuss and respond to requests for advice from distributors concerning the use of expressways and associated toll payment responsibility.
- 6Modal shift to marine and rail transport: For long-distance transport, we will use ferries or rail transport instead of trucks.
- 7Consideration of legal compliance when selecting contractual partners: We will select distributors in compliance with related laws and regulations.
- 8Safety measures when loading and unloading: We will clearly indicate safe job procedures, ensure safe pathways, take measures that include erecting scaffolding, and work to eliminate workplace accidents.
- 9Suspension/discontinuation of operations due to unusual weather, etc.: We will not make unreasonable transport requests amid typhoons or other unusual weather.
The White Logistics Movement is a key initiative of the National Action Plan for Realizing the Work-style Reform in the Motor Carrier Business that is being promoted mainly by the MLIT, METI, and MAFF. Shipping line and logistics service providers work together to contribute to economic growth by addressing the growing shortage of truck drivers and ensuring stable logistics necessary for people’s lives and industrial activities.
The key objective of the movement is to improve productivity of truck transportation and logistics efficiency while also striving to realize a labor environment that makes work easier for female drivers and those over the age of 60. We expect a number of good results from this initiative, including reducing our CO2emissions, and are particularly focused on creating good working environments for our workers.
Initiatives to Reduce the Environmental Impact of Logistics Operations
Along with conducting a modal shift*1 Daicel Logistics is working to reduce its energy usage and environmental footprint. Along with a modal shift from land to marine transport for imports and exports shipped between major ports and factories since FY2008/3, the company has worked hard to reuse containers.*2
For these efforts, in 2014 the company received the Logistics Grand Prize / Environmental Contribution Prize from the Japan Institute of Logistics Systems.
- *1The shift from truck-based goods transportation to more environmentally friendly marine and railway transportation.
- *2The practice of re-using devanned import containers for exports without returning them to the shipping companies.
Technical Training at the Safety and Quality Training Center
In 2011, Daicel Logistics Service opened the Safety and Quality Training Center on the premises of its Kansai Logistics Center Amagasaki Sales Office. This move was intended to step up its efforts to maintain distribution safety and quality, both essential to earning customer trust. Using its own curriculum, the Center conducts skill training for tanker truck drivers and on-site loading and unloading operators.
In FY2024/3, we conducted new training on transportation businesses for new drivers wherein participants learned about preventing the recurrence of past incidents and took practical tests in loading, unloading, and transporting. We also conducted online classroom learning and practical training in small groups to train the forklift operation skills of personnel in charge of loading and unloading cargo. These training programs were taught by experienced personnel and served as opportunities to pass on technical skills to younger workers.
In FY2024/3, we conducted 21 skill training sessions, and as of March 31, 2024, 1,517 workers had completed training.

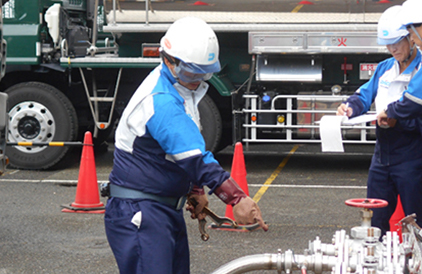
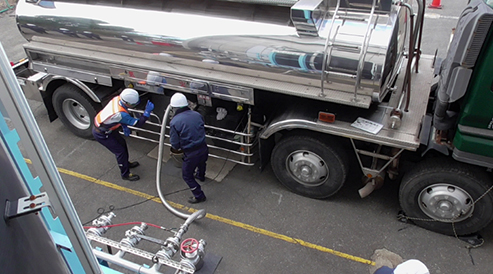