SustainabilityResponsible Care Activities
To practice the spirit of Responsible Care (RC), the Daicel Group established the Daicel Group Basic Policies for Responsible Care and is promoting across-the-board RC activities in the Daicel Group to contribute to the sustainable development of society.
Daicel Group’s Responsible Care
RC activities are undertaken by businesses that engage in the manufacture or handling of chemicals to preserve the environment and ensure health and safety at every stage of their operations, from product development, manufacture, distribution, and use to disposal. With chemical manufacturers around the world taking part in these efforts on a voluntary basis, the disclosure of results and dialogues with society are also positioned as key RC activities. Recognizing RC activities as one of the important social responsibilities of the Daicel Group, the RC Council, operating directly under Daicel’s president and CEO, commits to promoting the activities.
On February 21, 1995, the Daicel Group established its Basic Policies for Responsible Care (RC) based on “The Guiding Principles for the Improvement of Environmental, Health, and Safety Conditions” of the Japan Chemical Industry Association (JCIA) and supplemented the items on the preservation of biodiversity on April 1, 2011. Subsequently, the Policies were updated to the Daicel Group's Basic Policies for Responsible Care on April 5, 2017 in response to the revision of JCIA's guiding principles. The Basic Policies were established and revised with the approval of the President and CEO.
Daicel Group’s Basic Policies for Responsible Care
- 1In accordance with management policy, we will comply with laws and regulations and strive to safeguard the environment, health, and safety. For this purpose, we share specific implementation plans among all employees and put them into action.
- 2We will strive to continually improve environmental, health, and safety performance and the security of facilities as well as processes and technologies throughout the entire chemical lifecycle, from development to disposal, and inform society of the results of such efforts.
- 3We will further reduce our consumption of resources and energy and strive to reduce, reuse, and recycle waste.
- 4We will protect the environment and people’s health and safety by driving continual improvement in chemical product safety and stewardship throughout the supply chain.
- 5We will practice risk-based chemical management throughout the entire chemical lifecycle, from development and production to use, consumption, and disposal and strive to strengthen our chemical management systems by continual improvement.
- 6We will influence the employees and the value chain stakeholders to promote the safe management of chemicals within their own operations.
- 7We will strengthen our stakeholder relationships by understanding and responding to stakeholders’ concerns and expectations about safer operations and products as well as openly communicating about our performance and products.
- 8We will put the Daicel Group’s overall efforts into continually improving initiatives for the environment, health, and safety in order to meet stakeholders’ expectations.
- 9We will contribute to the sustainable development of society by developing and providing unique and innovative technologies and other solutions.
- 10We will promote biodiversity-friendly activities in order to pass on the wealth of nature to future generations.
Revised April 5, 2017
Promotion System for Responsible Care
In accordance with the Responsible Care Promotion Rules, the Daicel Group is implementing RC activities on the following fronts: occupational health and safety, process safety and disaster prevention, environmental preservation, chemical and product safety, distribution safety, and communication with society. The Daicel Group promotes these activities under the RC Council, which meets on a regular basis.
The RC Council is chaired by the officer responsible for the Safety and Quality Assurance Headquarters and is appointed to oversee RC by the President and CEO, who bears ultimate responsibility for RC activities. The council comprises, among others, the representative of the Daicel Workers’ Union Executive Committee and heads of administrative divisions appointed by the chairperson as well as the Responsible Care Center (RC Center) of the Safety and Quality Assurance Headquarters, which serves as the secretariat for the council.
Promotion System for Responsible Care
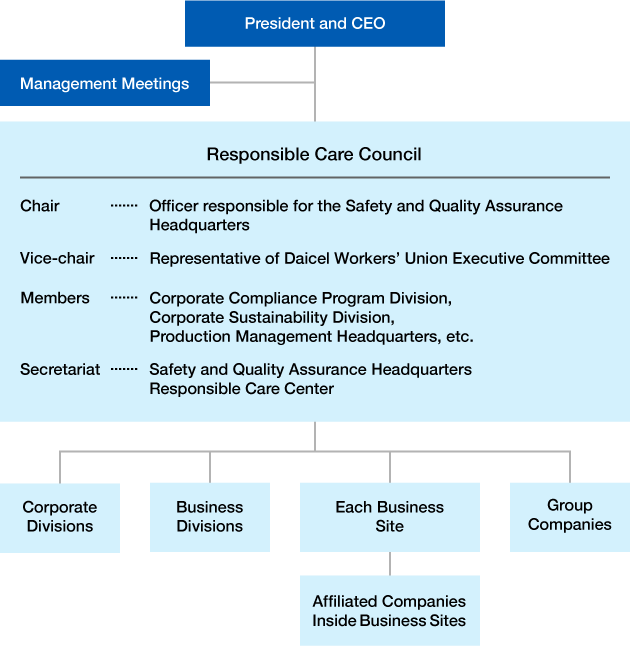
As of April 1, 2023, we have completed corporate reorganization aimed at strengthening our business infrastructure, which prioritizes safety, quality, and compliance.
Along with progressively dissolving the Quality Management Division and RC Division of the Assessment Headquarters, we established the Safety and Quality Auditing Division. The Safety and Quality Auditing Division will handle all operations involving auditing and education regarding safety and quality, which includes RC audits.
We also created the Safety and Quality Assurance Headquarters. The headquarters consists of the RC Center and the Quality Assurance Center and will manage and carry out all RC, quality assurance, and quality management operations. The officer in charge of the headquarters will serve as the chairperson of the RC Council and the manager of the Total EHS Assessment System and will oversee RC activities and Total EHS Assessment System initiatives.
Roles of the Responsible Care Council
In addition to formulating basic policies, the RC Council receives reports on RC activities from each business site of the Daicel Group at the end of the fiscal year and in turn reports to the Planning Meetings attended by management to propose targets and action plans for the next fiscal year, which are subsequently approved at the Management Meetings. The RC Council reports the status of the initiatives at the Management Meetings and conducts RC audits in accordance with the Rules on Responsible Care Audits.
Roles of the Responsible Care Council
Roles | Details |
---|---|
|
Formulate the Basic Policies for Responsible Care and set targets for the entire Group to steadfastly promote RC activities. |
|
Consider the necessary revisions to implementation systems to ensure effective operation of the CAPD* cycle, including setting targets, formulating implementation plans, and implementing and assessing the results of implementation. |
|
The council determines RC-related issues for the long-term plan and drafts for the RC medium-term plan by deliberating and deciding on important issues related to the entire Group and reviewing proposals submitted by the RC Center. |
|
The council deliberates on the RC implementation plan drawn up by the RC Center. After approval, it is deliberated by the Planning Meetings and approved by the Management Meetings. |
|
The council provides advice and guidance to the RC Center to effectively promote its activities. The RC Center conducts key issue discussions with the Environment and Safety Divisions, holds Site Safe Environment Managers Meetings, and strives to promote RC activities accurately. |
|
|
|
The council addresses RC activities deemed necessary in items other than 1. to 6. above. |
*Instead of a Plan, Do, Check, and Act (PDCA) cycle, the most widely known approach to continuous improvement, the Daicel Group has adopted a CAPD improvement cycle to avoid the risk of overlooking crucial facts and realities that often lie hidden in the initial planning stage.
Responsible Care Activity Audits
Audits by the Safety and Quality Auditing Division of the Assessment Headquarters
Consideration of Priority Responsible Care Issues
The RC Center promotes RC activities by discussing the progress in RC implementation plans, occupational health and safety, as well as process safety and disaster prevention, and the status of initiatives to address environmental concerns at Daicel and each domestic Group-company business site, and actively encouraging problem-solving.
In FY2024/3, in addition to the seven domestic business sites of Daicel Corporation, we visited the Fuji Plant of Polyplastics Co., Ltd.; the Iwaki Plant of Dainichi Chemical Co., Ltd.; all business offices of Daicel Logistics Service Co., Ltd.; the Okayama, Nagano, and Aomori plants of DM Novafoam Ltd.; the Isesaki Plant of Daicel Pack Systems Ltd.; Pi-Crystal Inc.; the Kameoka Plant of Daicel Beyond Ltd.; and Daicel Pyrotechnics Ltd., and discussed major issues.
CAPD Cycle
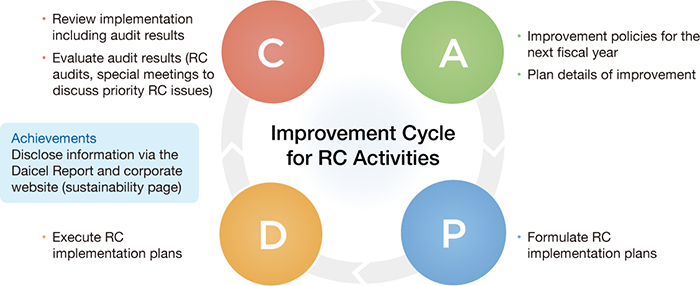
Promotion of Responsible Care Activities
Periodic Exchange Meetings for Supervisors of Environmental and Safety Divisions across the Group
The RC Center and individuals charged with supervising the Environment and Safety Divisions at Daicel’s business sites and the Fuji Plant of Polyplastics Co., Ltd. regularly meet in person and remotely for Safe Environment Managers Meetings. They also hold Group Company Safe Environment Managers Meetings with Dainichi Chemical Co., Ltd., Daicel Logistics Service Co., Ltd., DM Novafoam Ltd., Daicel Pack Systems Ltd., Pi-Crystal Inc., Daicel Beyond Ltd., and Daicel Pyrotechnics Ltd.
These meetings were held four times in FY2024/3, and participants exchanged information and discussed RC-related issues, such as occupational health and safety, process safety and disaster prevention, and environmental preservation, as well as the revised Industrial Safety and Health Act and other regulations.
Responsible Care Activity Good Conduct and Contributions Awards
Each year, the RC Council recognizes good deeds and contributions to RC activities. In FY2024/3, a member of the POM/Energy Group of the Production Department of the Fuji Plant of Polyplastics Co., Ltd. was commended. The recipient identified the source of the slight odor in the plant at an early stage and took countermeasures. In addition, by checking the soundness of other facilities through horizontal deployment, they contributed to the stable operation of the plant.
Internal Training and Education
So that all Daicel Group employees can understand the importance of RC activities and take action, we provide relevant in-house training and education.
Total Environmental, Health, and Safety Assessment System
Total Environmental, Health, and Safety Assessment System
The Daicel Group operates a Total Environmental, Health, and Safety Assessment System (Total EHS Assessment System) as a means for evaluating risk in its business activities.
The Total EHS Assessment System assesses the launching of new products in all business activities, including research and development, production, consumption, and disposal, as well as plans for modifying existing processes and equipment (new plans). Led by the general manager of the Safety and Quality Assurance Headquarters, the Total EHS Assessment System is a mechanism for conducting advance assessments of a diversity of risks across all business activities, covering everything from the environment to health and safety.
Overview of the Total Environmental, Health, and Safety Assessment System
- 1The system evaluates the new plan based on prescribed standards according to the format for eight items: legal compliance, chemical safety, environmental preservation, occupational health and safety, operational safety at facilities, product safety, distribution safety and safety of production outsourcing, and purchasing and sales.
- 2A new plan indicates all new changes that include the establishment and modification of facilities as well as changes in matters related to manufacturing, etc.
- 3The system defines two types of assessment: Corporate Total EHS Assessment, which covers new plans that may cause a significant impact on management, and Division Total EHS Assessment, undertaken by each division. After evaluating new plans based on their scale and risk with an overall assessment rank (I and II), the Group determines items subject to assessment, designates individuals to serve as assessment executors and final evaluators in accordance with the overall assessment rank, and records and stores assessment results.
- 4With regard to the adoption of a new process and/or increased production volumes, we carry out a Technical Assessment and Equipment Design Assessment, underscoring the importance of design specifications for technologies and facilities. After discussing the results of these assessments, a Corporate Total EHS Assessment is undertaken.
To achieve the aims of our medium-term strategies, with the goals of improving the precision and decision-making speed of new plans formulated throughout the company, we made revisions in FY2023/3, such as expanding the range of business site and SBU responsibilities, narrowing the scope of Corporate Total EHS Assessments for cases that could have a material impact on people’s lives or our business, and establishing Advisory Sessions to better utilize knowledge and technologies throughout the company.
In FY2024/3, we utilized the new assessment system to examine each new plan and hold Advisory Sessions. Including assessments of new plans from overseas production sites, the total number of Corporate Total EHS Assessments conducted since the introduction of this system stands at 1,148, and the number of Advisory Sessions has reached 15.
All of these assessment results are reviewed, and the assessment system is constantly evaluated to improve the accuracy of future plans.
Product Safety Assessments
For safety system-related products in categories such as pharmaceuticals, foods, cosmetics, healthcare equipment, and automotive products, the Daicel Group is enhancing its product risk assessments of product safety to ensure that it always provides customers with safe and reliable products. In FY2016/3, the Group began conducting Product Crisis Assessments, which identify and monitor product safety-related risks and review response systems for handling crises. Furthermore, in addition to conducting product safety-risk assessments internally, since FY2018/3 the Group has been holding Product Safety Advisory Meetings chaired by outside experts, to conduct assessments from an even more expert perspective.
In FY2024/3, there were no major product safety accidents that impacted the bodily health, lives, or property of our customers.
Total EHS Assessment Flow
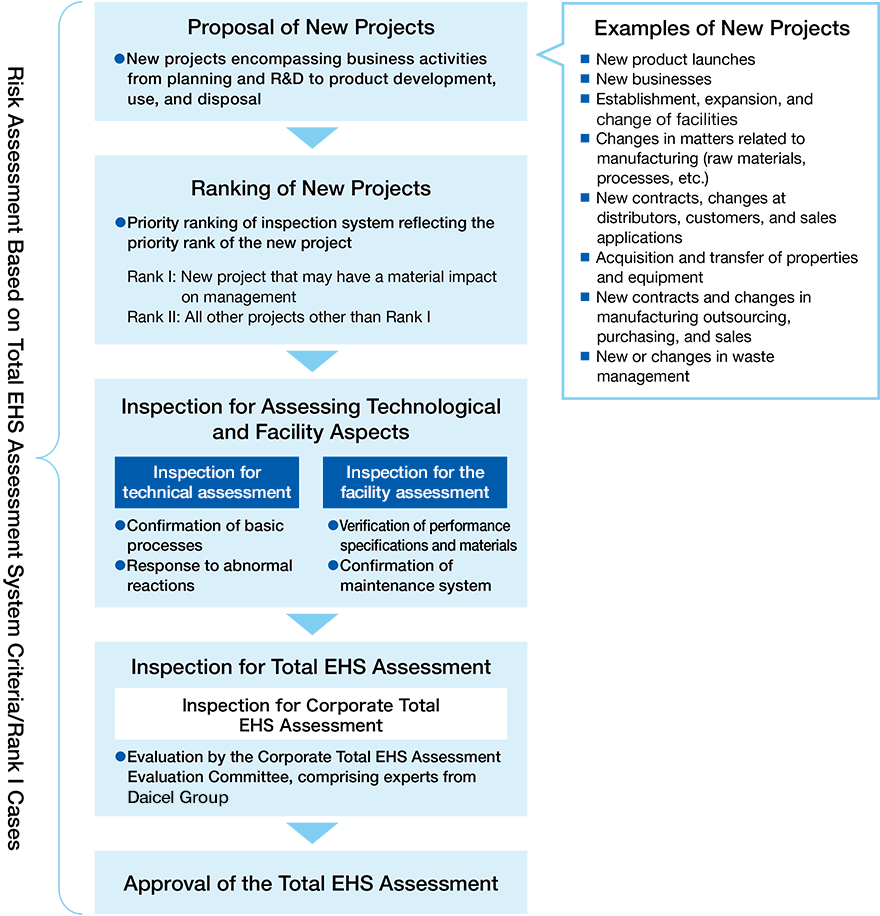
Breakdown of Total EHS Assessment System
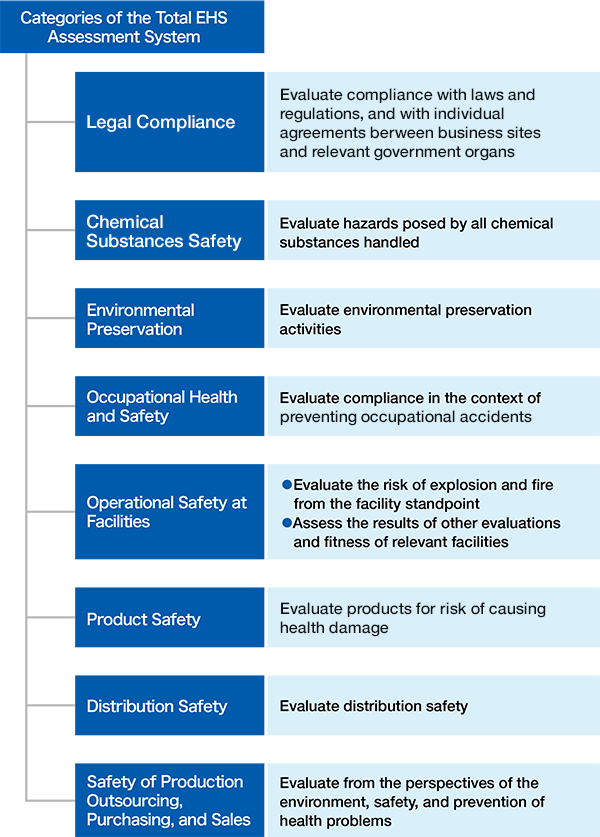
Responsible Care Global Charter
The International Council of Chemical Associations (ICCA), an international RC activity organization, put in place the Responsible Care Global Charter in 2005 with the aim of promoting sustainable development within the chemical industry while contributing to society as a whole through RC activities. Since it is in complete agreement with the goals and principles of the charter, Daicel became a signatory in 2008.
In order to more specifically detail the issues requiring attention with respect to the management of chemical product safety, improvements in the quality of life through the delivery and use of chemical products, and contributions to sustainable development in an easier to understand manner, the ICCA revised the charter in 2014. That same year, Daicel declared its support of the revised version of the Responsible Care Global Charter and confirmed its participation as an ongoing signatory again.
Declaration of Support for the Responsible Care Global Charter
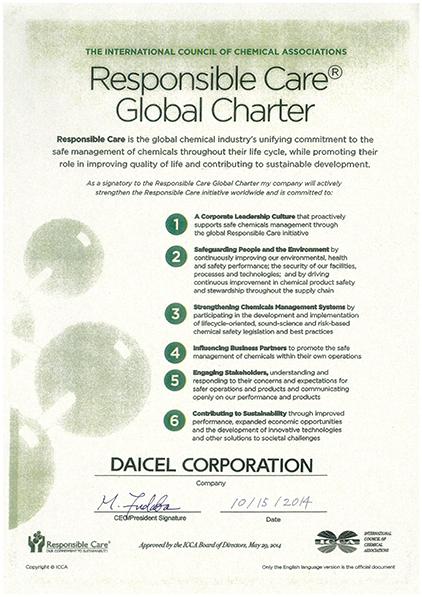
Websites of Each Responsible Care Activity
Responsible Care Management System
Environmental Preservation
- Environmental Management
- Response to Climate Change
- Information Disclosure in Line with TCFD Recommendations
- Reduction and Recycling of Industrial Waste
- Emission Management of Chemical Substances
- Water Resource Preservation
- Environmental Management and Prevention of Air Pollution
- Preserving Biodiversity
- ESG DataRefer to page 5 "Environmental Accounting."