HistoryDaicel’s cellulose
100 Years of Continually Evolving Technologies
For the more than 100 years since our founding, Daicel has been engaged in the research and development of the cellulose products we provide it to the world.
Even as we take advantage of the conventional properties of this material, we continue to create value by adding functions through chemical modifications and by combining cellulose with other materials.
The 100-year history of cellulose at Daicel
1919
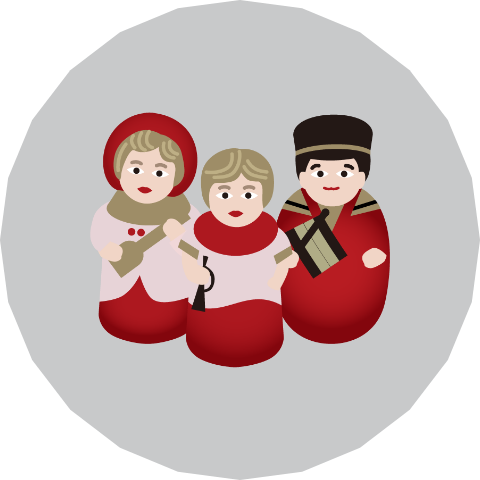
Dainippon Celluloid Co., Ltd. (the predecessor of Daicel) is established.
At the time, celluloid was the world’s first artificial plastic. Made mainly from cellulose nitrate and camphor, celluloid was in high demand all over the world. As competition for production intensified, eight manufacturers in Japan merged in order to prevent overharvesting of camphor trees, one of the raw materials; to eliminate excessive competition in the celluloid industry; and to promote the development of the processing industry.
1929
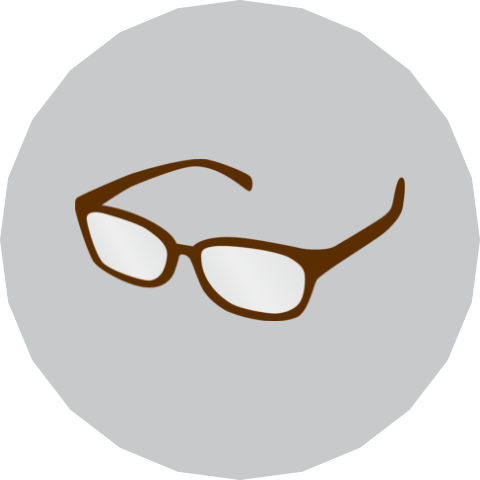
Although celluloid was a very useful plastic, it had the drawback of being highly flammable. To overcome this problem, the company developed acetyloid, an acetate plastic made from cellulose acetate, with the goal of offering a less flammable product.
1953
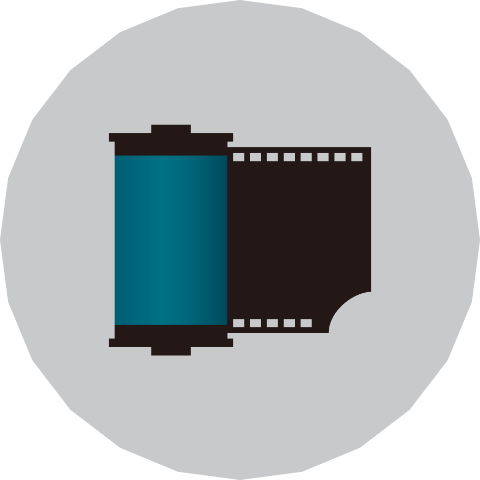
Tri-acetyl cellulose (TAC), a form of cellulose acetate used for photographic film, greatly contributed to the wide adoption of a safe form of nonflammable photographic film.
1958
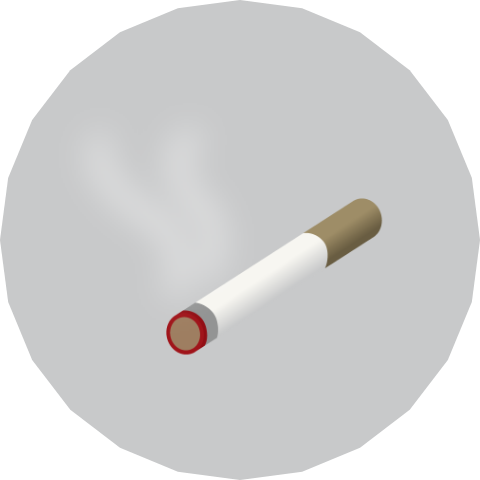
Several attempts had been made to remove the harmful substances from tobacco smoke as a means of protecting the health of smokers. Filters made of cellulose acetate were successfully adopted in the United States in 1951 because they adsorbed sufficient amounts of tar and nicotine without impairing the aroma or flavor of the tobacco. Later, in 1958, mass production began in Japan after an attempt at domestic production proved successful.
1982
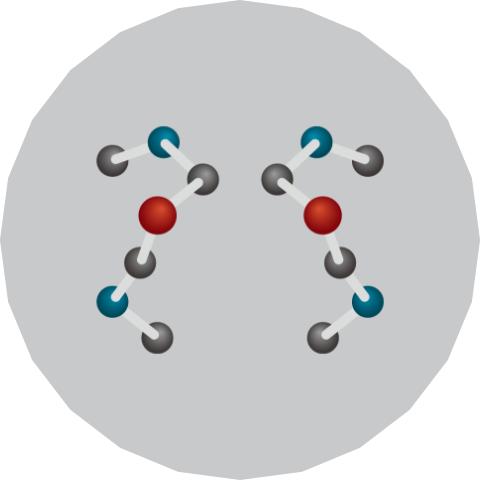
We introduced a chiral column with an optical isomer separation function that suppresses the side effects of artificially synthesized chemical substances. Thanks to its ability to distinguish cellulose molecules, this product is used to separate components that can be used effectively as medicines. It is widely used around the world as an indispensable tool for pharmaceutical R&D, manufacturing, and quality assurance.
1988
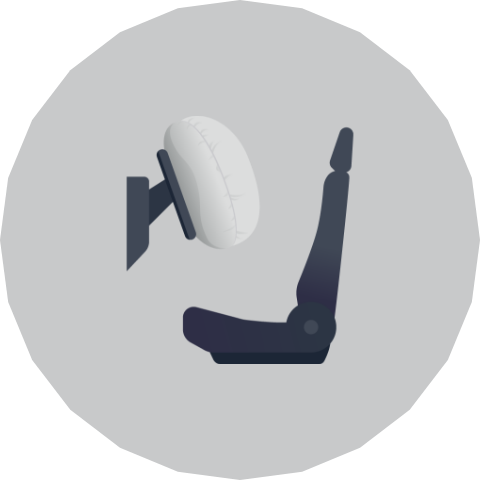
We began mass production of inflators, an important component of automotive airbag safety systems. Research and development of cellulose-nitrate-powered gas generators, which work safely and stably when needed, had begun earlier during the 1970s. The technology was then applied to pretensioner gas generators (PGGs) used with seat belts.
1990
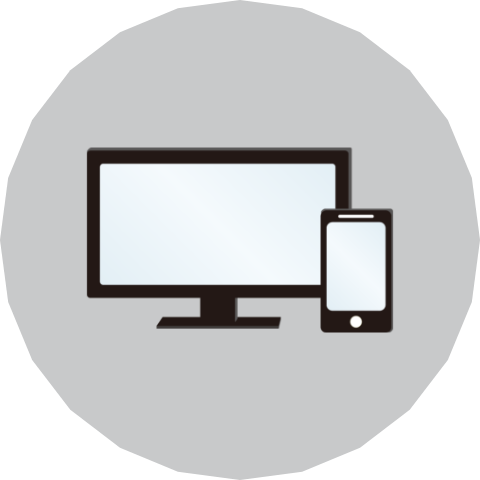
We began production of tri-acetyl cellulose (TAC) as an optical film for LCDs. TAC was originally developed as a base for photographic film, but its excellent flame-resistance, transparency, surface appearance, electrical insulating properties, and other characteristics expanded its scope of application, and it eventually became a component of LCDs to meet the needs of the digital age.
1994
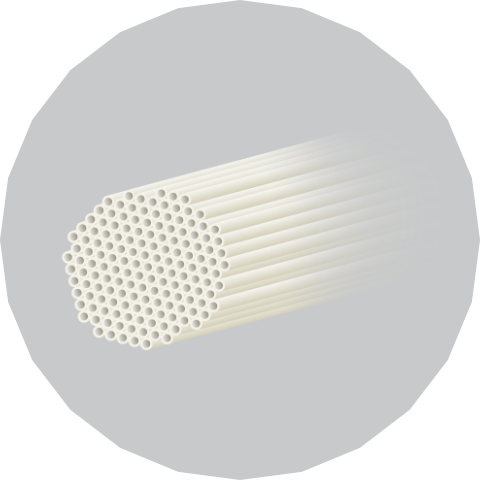
Water is a valuable resource that has become threatened as a result of climate change. We have introduced a separation membrane module for water treatment that can be used to treat water in a wide range of applications. Cellulose acetate is also used here as a membrane material exhibiting excellent hydrophilicity.
2019
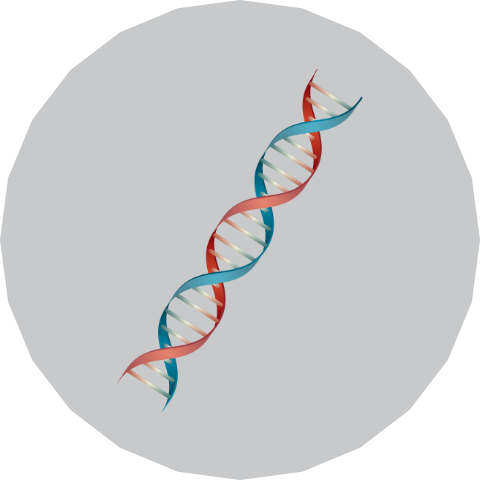
Actranza™ Lab is a new dosing device for animal experiments that instantly perforates the skin with a high-speed jet; thus, it uses no needle to introduce substances into the cells. This drug delivery system, which contributes to the emergence of innovative treatments such as gene therapies, uses the unique DAISI® energy system, a cellulose-nitrate-powered gas generator technology.
2021
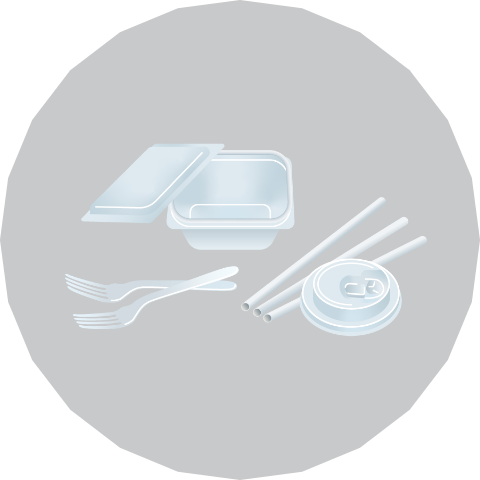
CAFBLO®, a cellulose acetate resin, dramatically improves the marine biodegradability of cellulose acetate. Cellulose-based plastics obtained from wood, cotton, and other inedible plants are expected to provide an effective solution to the global problem of marine plastic pollution.
Biomass Value ChainCreating value
through co-creation
Sustainable, recycling-oriented industrial ecosystems
The Biomass Value Chain Concept
In an effort to create a sustainable recycling-oriented industrial structure grounded in cellulose processing technology, we are advocating the Biomass Value Chain Concept. Using forests, which account for about 70% of Japan’s land area, as a raw material, this approach of revitalizing the local economy by linking the chemical industry as well as a wide range of primary and secondary industries requires empathy as well as a co-creation approach involving extensive technology sharing.