About the Micro Plant
Producing what is needed without waste.
The Micro Plant, a revolutionary ultra-low-energy production system
Large-scale, high-energy conventional manufacturing method
before
The chemical-making processes in conventional chemical plants use high-energy processes in which large volumes of materials are placed in huge reactors, large amounts of heat and pressure are applied, and molecules react while being heated for long periods of time. In large reactors, the temperature and pressure become uneven, and many undesirable compounds are produced, so additional energy is required to remove them. The “micro plant,” is a technology for making ultra-compact plants by combining single glass plates that fundamentally overturns a process that requires a lot of energy and processes.
Image of the inside of a kiln at a general chemical plant

The Micro Plant — the ultimate ultra-low-energy plant
after
In a Micro Plant, materials flow in approx. 100 μm ultrafine channels (flow paths) extending throughout a 7 × 3 cm glass plate.
Molecules meet with pinpoint precision at an even temperature and pressure, and reactions occur in a much shorter time than before. Furthermore, undesirable components are not generated, and thus a process to remove them is no longer required.
It is the ultimate ultra-low-energy plant that significantly reduces CO₂ emissions by lowering energy consumption and contributes to carbon neutrality.
Reaction in a Micro Plant

Process change that occurs when a resist polymer plant for semiconductors, etc., is converted into a Micro Plant and the industrial revolution that occurs when the entire supply chain is converted into Micro Plants
[1] Converting a conventional resist polymer plant into a Micro Plant
- Conventional resist polymer plant process
- Process after conversion into a Micro Plant
The purity of the initial reaction is high, so there is no need for post-processing.
[2] Additional conversion of the entire supply chain into Micro Plant
- Conventional monomer manufacturing process
- Conventional solvent manufacturing process
- Supply chain process innovation after full conversion into Micro Plant
Post-processing is no longer required at any plants, so an ultra-efficient supply chain is created.
Three production revolutions of the Micro Plant
Microminiaturization revolution
In the case of the Micro Plant, each unit is completed by connecting small glass plates called microfluidic devices in series. By integrating the designs for the glass flow paths, the Micro Plant can handle any chemical product, and the production volume can be increased limitlessly by arranging units in parallel.
For example, a large 20 m × 20 m × 20 m plant can be microminiaturized, even to desktop scale. In addition, when industrializing the results of laboratory experiments, the results can simply be replicated with an increased number of glass plates. Microminiaturization affects not only the scale and production efficiency but also eliminates waste in the research to implementation process.
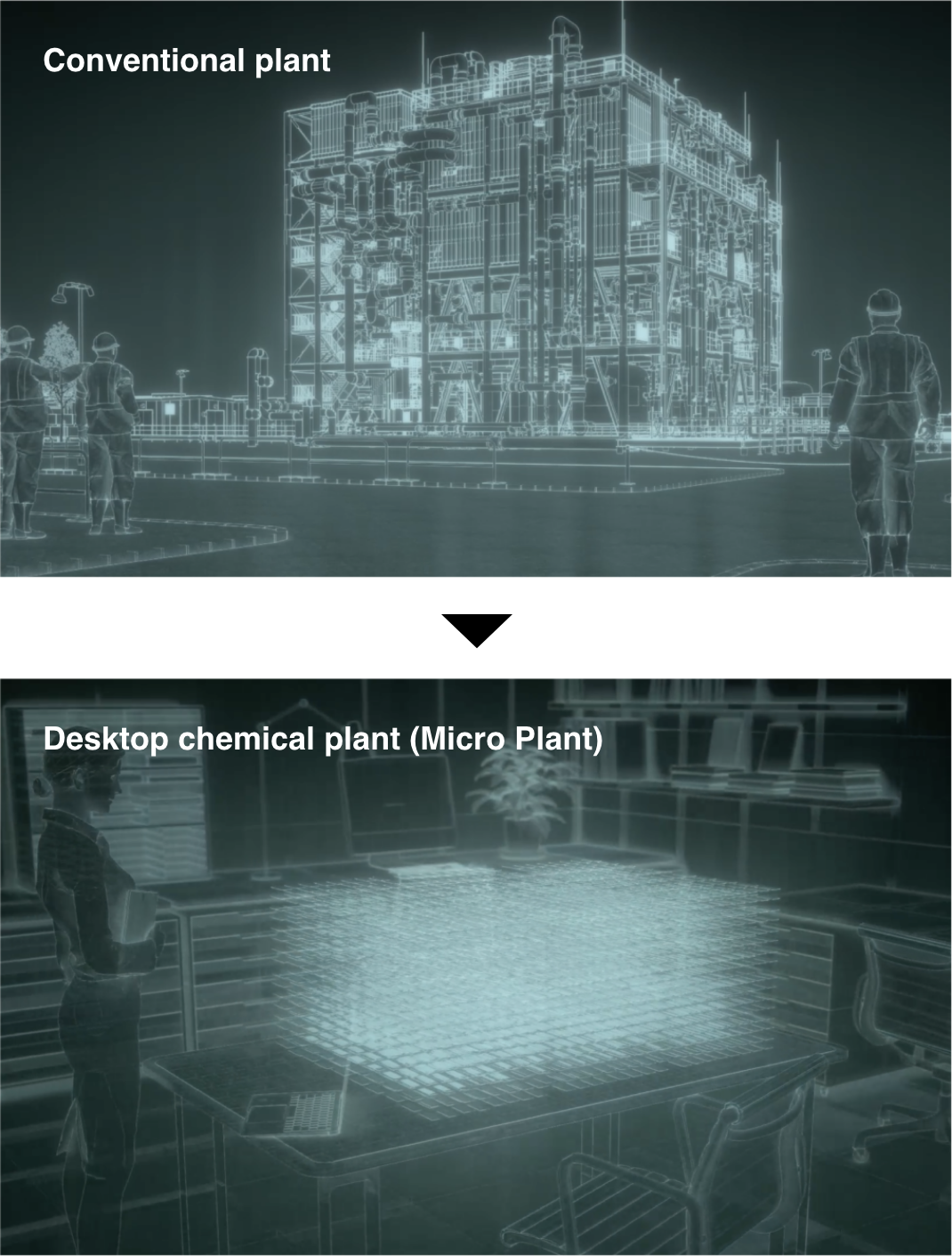
Ultra-low-Energy revolution
In ultrafine flow paths, it is possible to produce targeted reactions quickly with pinpoint precision at an even temperature and pressure. Since wasteful reactions are unlikely to occur, the purity of the product is high, and there is no need for post-processing to separate out undesirable components. This can reduce energy consumption and CO₂ emissions by more than 90%.
Production facility revolution
Because the Micro Plant is ultra-small, ultra-low-energy, and low cost, it drastically increases the flexibility of production facilities. If production facilities are located where the raw materials are, local production for local consumption is easier, and the cost and energy required for transportation can be reduced significantly.
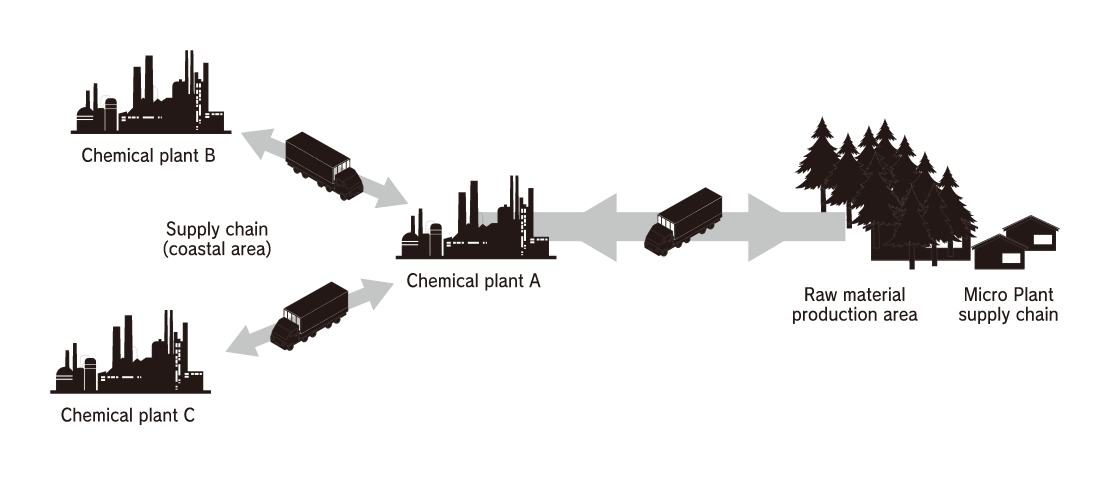