Research & Technology Development Production & Process Technology
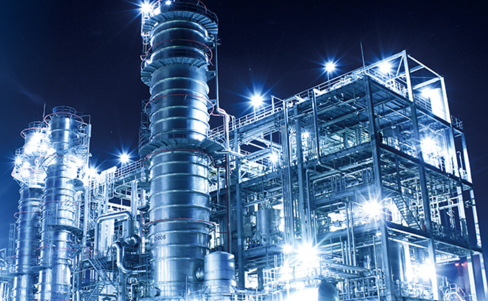
We believe that a chemical company must not only make products that benefit people and society, but also ensure that its manufacturing process is friendly to people, society, and the environment. Based on the DAICEL Production Innovation, we are enhancing our competitiveness as a manufacturer through process innovation and energy innovation, and are challenging ourselves to realize a decarbonized society throughout the entire supply chain.
DAICEL Production Innovation + DX
We will work on innovating the operation and running of the entire factory while maintaining the current manufacturing processes and facilities.
DAICEL Production Innovation
DAICEL Production Innovation is our fundamental approach to manufacturing in which the operation and management of entire plants is optimized to dramatically improve productivity. We are establishing a system to visualize and standardize the expertise accumulated through the operation of chemical plants, supporting decision-making for on-site operators.
Autonomous Production System
This system is an evolution of "Daicel Production Innovation" utilizing AI. It features mechanisms for deriving optimal operating conditions and detecting deviations from plans to make necessary corrections. This contributes to further improving productivity and stabilizing plant operations.
Process Innovation
After thoroughly pursuing improvements through "Daicel Production Innovation," we approach the innovation of existing manufacturing processes and equipment from the perspective of plant engineers.
Modified Petlyuk distillation process・VRC Technology
In the chemical industry, a significant portion of energy is consumed in the recovery process to remove impurities. To reduce this energy consumption, we have developed and implemented our own proprietary process technology.
Microfluidic Device Plant
We are working on realizing the next-generation production plant using "microfluidic device technology," which enables chemical operations such as mixing, reaction, and purification of substances within hair-thin channels etched into a 7×3 cm glass plate. Since the recovery process required for mass production becomes unnecessary, it allows for large-scale production using the same methods established in research fields. At the same time, it achieves space-saving, energy-saving, and resource-saving production while manufacturing only the necessary amount of materials as needed.
Biomass Value Chain
We are applying technology that enables the complete dissolution of wood to create a system for circulating forests, which cover approximately 70% of Japan’s land, as a renewable resource. By collaborating with like-minded partners across industries and sectors, we aim to optimize manufacturing across the entire value chain and build a sustainable, circular society.
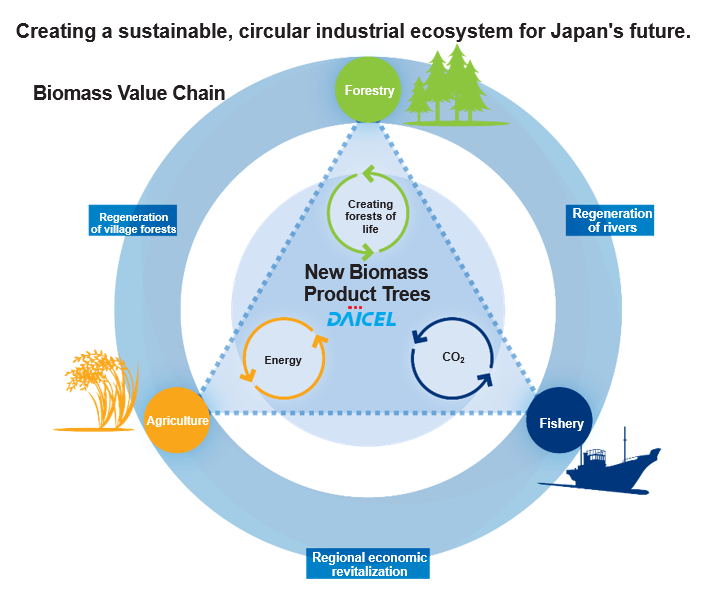
Energy Innovation
In DAICEL Production Innovation, we visualize energy usage in manufacturing and operate plants optimally from an energy perspective. We aim to expand the optimal range of energy utilization and pursue overall optimization of energy use across multiple plants.
Virtual Factory
We aggregate and manage operational data from two geographically separatedplants—Aboshi Plant (Hyogo Prefecture) and Otake Plant (Hiroshima Prefecture)—to implement optimal production planning and energy supply-demand balance for both sites, effectively creating a "virtual factory."
As part of optimizing energy supply and demand, the Ohtake Plant started sending excess generated electricity to other worksites in West Japan using the self-consignment system. The plant began sending electricity to the Arai Plant in East Japan and to the Fuji Plant of Polyplastics Co., Ltd. Looking ahead, we expect to further extend the system to other Group companies toward achieving zero purchased electricity at the Group level.
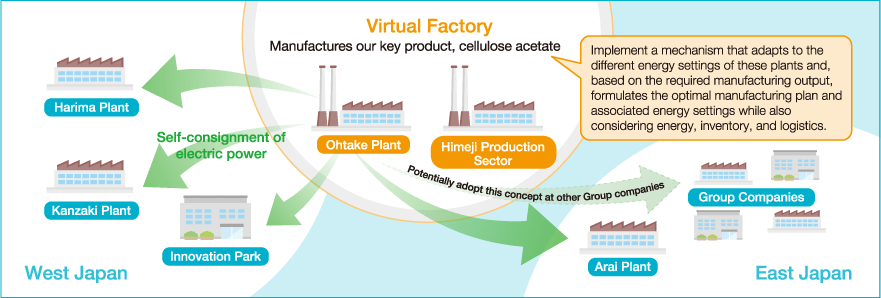